学而优则仕 达者善天下
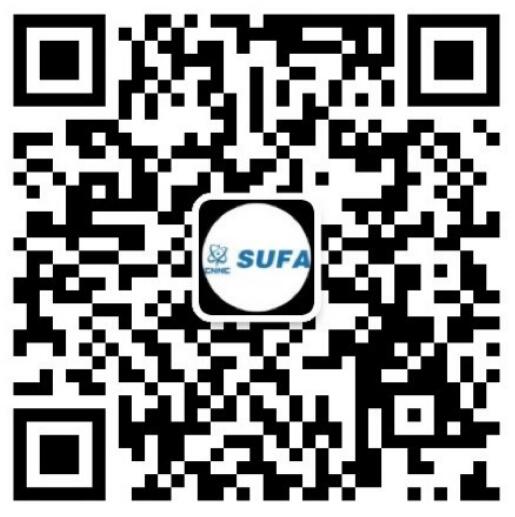
Quality Assurance
Training system
In order to continuously improve the quality awareness of all employees of CNNC SuFa valve Company, make them fully aware of the importance of product quality, and improve the professional level of various personnel, CNNC SuFa Company conducts a series of training and education activities every year to provide all employees with education and training on quality management standards, regulations, basic knowledge of quality management, quality awareness, and business knowledge, ensuring that all employees receive training, The certified employment rate is 100%, which continuously improves the quality of personnel, enhances their awareness of valuing quality, and further unleashes their subjective initiative, enthusiasm, and sense of responsibility.
Detection
Process control and inspection are the two main aspects of quality control. CNNC SuFa valve Company has complete testing methods and possesses non-destructive testing equipment such as ultrasonic flaw detectors, radiographic flaw detectors, accelerators, and magnetic particle flaw detectors. The company also has physical, chemical, and metrological testing equipment such as material analysis direct reading spectrometers, high/low temperature material testing equipment, metallographic microscopes, coordinate measuring machines, and platinum measuring arms. The company conducts incoming inspection and testing, The process inspection and testing of the production process, until the final inspection and testing, have been formulated and implemented with guidance documents related to inspection and testing. Inspectors carry out inspections throughout the production and manufacturing process according to this, and full-time quality assurance personnel track and verify according to the prepared quality plan.
Personnel Assurance
In order to ensure the normal and effective implementation of valve production and quality assurance activities, CNNC SuFa Valve Company has set up a quality administrator in each workshop according to the actual situation, specifically responsible for the quality control work of the workshop, monitoring and supervising the quality control points, and also responsible for the analysis, research, and implementation of improvement measures for non conformities in the workshop. In the field of nuclear power, the company has also set up a professional quality assurance engineer for nuclear power, responsible for reviewing technical documents, records, and reports within the scope of this profession, ensuring the completeness and accuracy of documents, reports, and data, and ensuring that the company's quality assurance responsibility is implemented to individuals, creating good conditions for closed-loop management of quality assurance work.
In order to control the review and disposal of non-conforming products in valves, CNNC SuFa Valve Company has established a dedicated non-conforming product handling team, mainly composed of design, process, and quality management departments. In handling non-conforming products, we adhere to the principle of "three not letting go", that is, "not letting go if the cause cannot be found, not letting go if the responsibility is not clear, and not letting go if the improvement measures are not implemented." To avoid the recurrence of quality problems. Quality records are a true record of quality control in the production process and an important basis for quality traceability management. In the process of collecting, organizing, and archiving product quality records, CNNC SuFa adheres to the principle of "software and hardware synchronization", which means that product quality records and products are stored simultaneously.
In order to verify the implementation and effectiveness of the quality manual outline, CNNC SuFa Valve Company conducts two internal audit activities per year based on the prepared internal audit plan, and conducts an annual management review at the beginning of the following year. The responsible department formulates and implements corrective measures for the proposed non conformities. The quality assurance department verifies the completion of the measures, ensuring that the company's quality system operates normally, is suitable, sufficient, and effective.